Assembly line robots are nothing new in the world of mass manufacturing, having been around for decades. Repetitive, menial tasks assigned to robots has been the normal cost saving measure for a while, especially seen in automotive and food processing in large scale businesses.
While this has enabled the factory worker to be better deployed, collaborative robots – or ‘cobots’ are a new trend in workplaces that may see the four-day work week become a reality.
One of the many stress point factors that the Covid-19 pandemic raised was the reliance and recognition of the importance of the value of people in the workplace. This is not to suggest this was not important pre-pandemic or devalued, but during the pandemic employee health and wellbeing was weighted differently to the norm, and terms such as flexible work schedule, and work life balance, became more common place as people shifted to a new norm.
As a result of this, many workplaces of varied sizes started trialling four-day work weeks, in an effort to sustain and manage employee safety while maintaining corporate KPIs and outcomes. Now with a labour gap in the marketplace and with industry struggling to maintain employees, it is time to address the supply chain and productivity issues facing mass manufacture today.
In the UK and within manufacturing in particular, the Manufacturing Technology Centre in Coventry Has offered a four-day week to 820 of its technical staff, following a two year “Fully Flexible Working Week” trial where 50% of employees responded with higher productivity. This allows for longer shifts over fewer days to maintain working hours had they worked five.
Mark Gray, of Universal Robots discusses how cobots could help make the four-day work week a reality for manufacturing professionals by increasing productivity whilst also facilitating reduced hours, in turn improving job satisfaction.
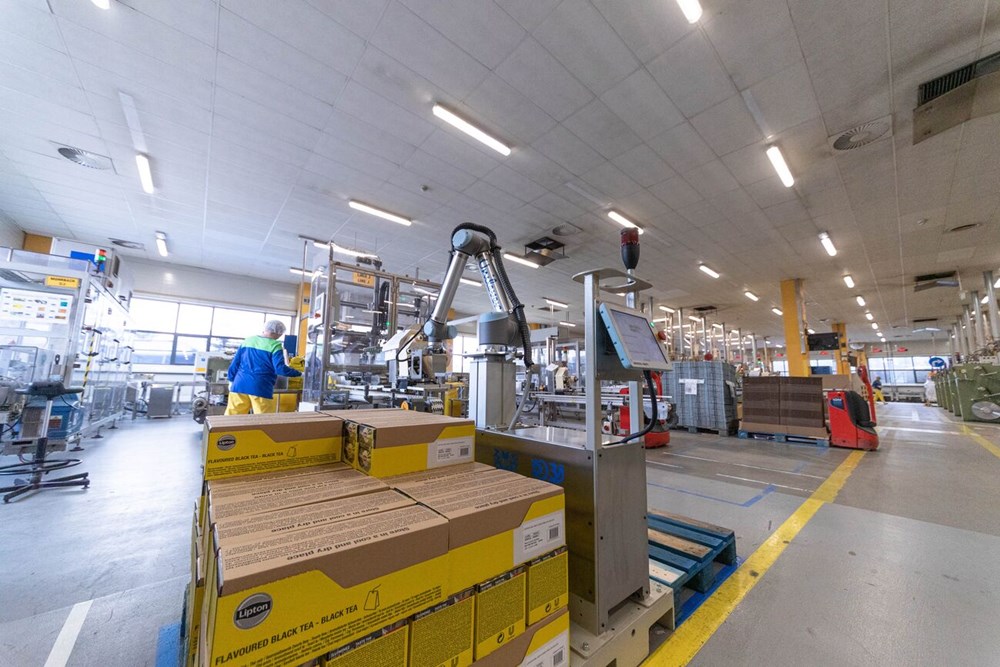
Universal Robots began life within Odense University in Denmark where three friends researched how industrial robotics could be deployed within SMEs. Barriers relating to cost, time and complexity of operation have made traditional robotics cost-prohibitive for SMEs to deploy. Thus, the concept of collaborative robots was born – robots that can give manufacturers access to all the benefits of advanced robotic automation, without the extra costs, difficult programming, long set-up, and shielded work cells – making automation affordable for small-batch production runs and mixed product assembly.
“Cobots differ in that traditional automation is usually a long, drawn-out process for a company to adopt, and there is lots of design stages, and ultimately a build stage. Our robots, however, can be deployed within a matter of weeks, and can therefore save money straightaway. The basic advantages of cobots for manufacturers is that they are very quick to setup, easy to programme, and flexible enough to be moved around the factory as they do not necessarily need guards around them. Now is the opportunity for using robots in tasks that have never been automated before. We talk about the 3D jobs – dirty, dangerous, and dull, and it is surprising how many tedious tasks are still being performed by people.” Mark explained.
A four-day work week, achieved through collaborative automation, can ensure workers no longer need to spend time on menial factory tasks. By working with cobots, employees can then focus their time on more fulfilling roles, and reduce their time spent at work, improving overall wellbeing. This includes getting rid of the night shift, known to have an adverse effect on the health of workers.
For all industries, keeping your employees happy and fulfilled matters. That is why ABM’s modular approach ensures you pay for the packages your business needs rather than a flat bundle of unusable software. See how ABM can make a difference for your business today.